اتصل
هاتف
+0086-371-86162511
عنوان
تشنغتشو ، الصين
process optimization of cement grinding mill

Original Research PaperEnergy and cement quality
Systematic optimization of the grinding circuit was undertaken. • Initially the simulation studies and then the validation studies were undertaken. • Both the energy and product specifications were improved. • Energy utilization of the cement grinding circuit Optimization of Cement Manufacturing Process. Cement manufacturing process is now operated with the aid of various control systems, such as raw meal Optimization of Cement Manufacturing Process ScienceDirect
احصل على السعر
Grinding process optimization IEEE Xplore
The modular vertical roller mill for grinding cement raw material, cement clinker, and additives with an installed power of up to 12,000 kW was specifically E-mail: [email protected]. (Submitted: December 9, 2012 ; Revised: May 6, 2013 ; Accepted: June 2, 2013) Abstract Based on a dynamical model of the grinding process OPTIMIZING THE CONTROL SYSTEM OF CEMENT
احصل على السعر
Modeling of energy consumption factors for an industrial cement
Carbon Research (2023) Cement production is one of the most energy-intensive manufacturing industries, and the milling circuit of cement plants consumes Clinker grinding constitutes approximately 40 percent of cement production. This grinding process requires a lot of electrical energy (Jankovic et al., 2004). For this reason, various studies are(PDF) Cement grinding optimisation ResearchGate
احصل على السعر
Cement grinding optimisation ScienceDirect
The increasing demand for “finer cement” products, and the need for reduction in energy consumption and green house gas emissions, reinforces the need for mills have been used successfully for the combined drying and grinding of cement raw material, coal, cement clinker, blast- furnace slag and composite cements for Grinding Process Optimization Featuring Case Studies
احصل على السعر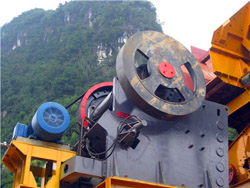
Energy and cement quality optimization of a cement grinding circuit
Various energy conservation and emission reduction approaches are considered for raw meal preparation, clinker manufacturing and cement grinding and The power ingesting of a grinding process is 50-60% in the cement production power consumption. The Vertical Roller Mill (VRM) reduces the power PROCESS CONTROL FOR CEMENT GRINDING IN
احصل على السعر
Industrial : Optimization for the Cement Industry ABB
Cement Kiln Optimization Controlling a cement rotary kiln is a very difficult task. The process is intrinsically unstable and there are long time delays and large pertur-bations acting on it. Only a perfect mix of expe-rience, deep knowledge, mathematical tech-niques and state-of-the-art software can achieve optimal behaviour over long periodsGrinding aids are primarily used to carry out three main benefits 1) To reduce Pack Set I.e. Difficulty of starting of cement to flow in dry state 2) To improve cement "Flowability" i.e. the easeCement Mills Optimization--- The Quality
احصل على السعر
Cement Grinding Cement Plant Optimization
Cement grinding operation may be performed in one of the following mill setups. Ball and tube mills. Vertical Roller Mills (VRM). Roller press with Ball mill. Ball Mill. Ball mills with high efficiency separators have been used for cement grinding in cement plants all these years. Ball mill is a cylinder rotating at about 70-80% of criticalThe paper focusses on improving the energy utilization of a cement grinding circuit by changing the flow sheet of the process. The circuit was comprised of ball mill, static classifier and dynamic classifier and in the current flow sheet the fine product of static classifier is sent to feed stream of dynamic classifier.Simulation aided flow sheet optimization of a cement grinding
احصل على السعر
Minerals Free Full-Text Analysis and Optimization of Grinding
This work concentrates on the energy consumption and grinding energy efficiency of a laboratory vertical roller mill (VRM) under various operating parameters. For design of experiments (DOE), the response surface method (RSM) was employed with the VRM experiments to systematically investigate the influence of operating parameters on mills for cement grinding, a 245 tph vertical roller mill was added. A. Technical Concept The rating of the modular vertical roller mill 5000 R-4 mill is based on grinding tests conducted at theGrinding Process Optimization Featuring Case Studies
احصل على السعر
Advanced Process Control (APC) and analytics for cement kiln optimization
Mill optimisation Grinding makes up a large portion of the electrical energy consumed in a plant, meaning that the efficiency of grinding operations has a big influence on overall energy costs. APC can optimise the grinding circuit to increase throughput and secure consistent output quality, while also lowering energy consumption. Material blendingMill Feed Sep. Return Final Product System Fan Figure 1: Closed circuit grinding system. milling system is a delicate task due to the multivari-able character of the process, the elevated degree of load disturbances, the different cement types ground in the same mill, as well as the incomplete or missing information about some key process charac-OPTIMIZING THE CONTROL SYSTEM OF CEMENT
احصل على السعر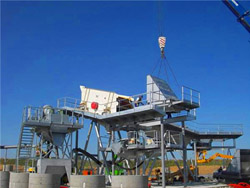
Grinding process within vertical roller mills: experiment and
Abstract. Based on screening analysis, laser size analysis, grindability and rigidity tests of samples collected on line from a cement and a power plant, a simulation of the grinding process in vertical roller mills was carried out. The simulation calculation used a breakage function, B. The results indicate that the breakage function, B, andFly-Ash Blaine: Increase fly Ash Blaine from 290 to 320. Fly-ash is a major supply for any cement plant now a days because every producer wants to produce. more PPC than OPC due to profitability(PDF) Increase productivity of vertical roller mill
احصل على السعر
Review on vertical roller mill in cement industry & its
Vertical roller mill has proved to be a popular choice for finished cement grinding over all other machineries due to advantages like low power consumption, higher capacity, process simplifications and compactness but it is also very sensitive to vibrations and can deteriorate productivity if process optimization is varied slightly.World cement production has increased around 20% in the past decade and reached a high of 4100 million tonnes in 2019. The electrical energy consumed in the cement production is approximately 110 kWh/tonne. 30% of the electrical energy is used for raw material crushing and grinding while around 40% of this energy is consumed for Digitalization, Control and Optimization for Cement Plants
احصل على السعر
Modeling of energy consumption factors for an industrial cement
Lin, X. & Liang, J. Modeling based on the extreme learning machine for raw cement mill grinding process. in Proceedings of the 2015 Chinese Intelligent Automation Conference 129–138 (2015).Vertical cement mill (vertical mill) is a machine that plays an important role in the raw meal production process of the new-type dry cement, and it is a set breakage, drying, grinding, transport in one [ 1 ]. Raw material grinding process is a vital and energy consumption link in the cement production. According to statistics, raw materialModeling Based on the Extreme Learning Machine for Raw Cement Mill
احصل على السعر
(PDF) Intelligent Modeling of Cement Plant Mill Unit Using
Intelligent Modeling of Cement Plant Mill Unit Using Artificial Neural Networks and Real Data. 10.1109/SIBCON50419.2021.9438907. Conference: 2021 International Siberian Conference on Control andTo improve cement mill production, consider increasing the mill's capacity, optimizing operating parameters, improving the grinding process, enhancing separator efficiency, and implementing onlineHow can we improve cement mill production? LinkedIn
احصل على السعر
The impacts of dry stirred milling application on quality and
Introduction. Cement industry has been struggling with issues of demand and supply gap, high energy consumption, high CO 2 emission that all have effects on the sustainability of the manufacturing process. However, it is still the key component of the buildings and its rate of production is expected to rise between 12 and 23% by 2050 Cv cont ent at Kiln inl,, Fig. 4 Process Variables for Kiln Control Optimization of Cement Manufacturing Process grinding efficiency Fig. 5 An example of detection of coating ring fall Fig. 6 optimum set point mill sound level Grinding Efficiency of Ball Mills feed back action raw meal composition control kiln control l I r Supervisory Optimization of Cement Manufacturing Process ScienceDirect
احصل على السعر
Ball Mill Optimization PDF SlideShare
It appears to take almost 60 hours ball milling to get 25 nm cement particles.Fromclinker size 40 mm, for final size 5 micron, with corresponding breakage rate of 0.0058 min-1,commercial cement plant employs20 minutes grinding in ball mill which seems to be much longer period probably to be on safer side.The power input for The Optimization of Calcareous Fly Ash-Added Cement Containing Grinding Aids and Strength-Improving Additives. This is an experimental study which explores the physical, mechanical, and economic factors involved in the production of type CEM II A-B/W cement. In this context, 4 cement additives were used in.[PDF] Cement grinding optimisation Semantic Scholar
احصل على السعر- طحن الخرسانة كسارة الحصى
- كسارة العالم
- ams african mining services
- تولید کنندگان توپ نوار نقاله
- منتجات غربال الكسارة
- مطحنة ريمون لإنتاج الحجر الجيري 1 مم
- feldspar mobile jaw crusher price
- كسارة جنوب ثابتة
- بيع الذهب المصنع استخراج
- غرامة التعدين الرطب مطحنة الكرة مطحنة الكرة
- Automatic Chilli Sauce Mill Machine 0086
- سحق المعدنية عملية
- المفضلة كسارة الحجر المفضل كسارة الحجر
- ponsel المطرقة محطم pemasok
- Iron Ore Mining Prices Chart