اتصل
هاتف
+0086-371-86162511
عنوان
تشنغتشو ، الصين
flow chart of iron ore pellet plant process
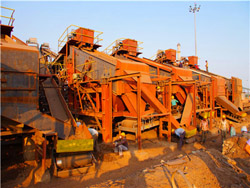
(PDF) Iron Ore Pelletizing Process: An Overview
Figure 2 shows a flowchart of a typical pelletizing plant, highlighting the additive preparation, mixing and pelletizing feed The iron ore pelletizing process consists of three main steps: Pelletizing feed preparation and mixing: the raw material (iron ore Iron Ore Pelletizing Process: An Overview
احصل على السعر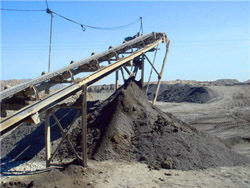
Iron Ore Pelletizing Process: An Overview IntechOpen
The iron ore pelletizing process consists of three main steps: Pelletizing feed preparation and mixing: the raw material (iron ore concentrate, additives There are two main technologies/processes for producing iron ore pellets: The Grate-Kiln System and the Straight Grate System. The First Grate Kiln System pellet plant was installed in...Process flow diagram of pelletization unit
احصل على السعر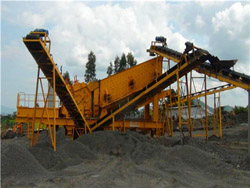
KOBELCO Pelletizing Process
There are two major methods of ironmaking: (1) ironmaking on large-scale using a blast furnace and (2) ironmaking on small-to-mid scale using an electric arc Context 1 process consists of proportioning system, mixing, pelletizing system, green ball roller screen, and distribution, as well as grate-rotary kiln system for pellet indurations,...Process flow chart of grate-kiln pelletizing plant.
احصل على السعر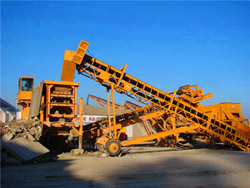
Process flow chart of preparation of pellets
Download scientific diagram Process flow chart of preparation of pellets from publication: Pelletisation Behavior of Fluxed Iron Ore Pellets of Varying Basicities Made with Waste Fines |...The iron ore production has significantly expanded in recent years, owing to increasing steel demands in developing countries. However, the content of iron in ore Iron Ore Pelletizing Process: An Overview Semantic Scholar
احصل على السعر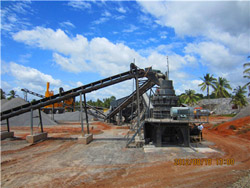
Flowchart of the pelletizing operation. Download
Context 1 the arrival, the slurry is stored in tanks and distributed to thickener (42 m), where its function is to densify the slurry (up to 69% solid) and route this material downstream the...A brief introduction to recent developments in iron ore pelletizing is provided in this chapter, including the world output of fired pellets, pellet production processes, preparation of pellet(PDF) Iron ore pelletization ResearchGate
احصل على السعر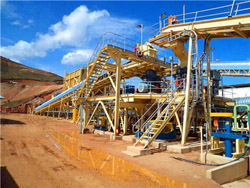
Flowchart of the pelletizing operation. Download
Size of the fired iron ore pellets is a critical variable, being normally controlled between about 8 and 18 mm. Pellets that are finer than this are undesired, since they will reduce permeabilityThe Ambient Compressive Strength (CS) of pellets, influenced by several factors, is regarded as a criterion to assess pellets during metallurgical processes. A prediction model based on Artificial Metals Free Full-Text Prediction Model of Iron
احصل على السعر
Characterization and Beneficiation of Dry Iron Ore
Characterization and Beneficiation of Dry Iron Ore Processing Plant Reject Fines to Produce Sinter/Pellet Grade Iron Ore Concentrate P. Dixit1 & D. Makhija1 & A. K. Mukherjee1 & V. Singh1 & A. Bhatanagar2 & R. K. Rath3 Received: 6 September 2018 /Accepted: 12 September 2018 /Published online: 18 September 2018The haematite ore in South Africa is processed in a dry process to a HQ lump ore with 64 % iron content and a sintered fine ore with 63.5 % iron content. For fine ore beneficiation, wet processes are used. Capacity at the Minas Rio is to be increased from 26.5 Mta capacity to 28 Mta in the forthcoming years.Dry beneficiation of iron ore Mineral Processing
احصل على السعر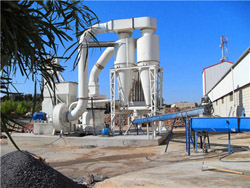
Comminution and classification technologies of iron ore
There have been three expansions since, and in the 1990s Empire Mines had a total of 24 individual concentrating lines and a total plant capacity of 8 Mtpa of iron ore pellets. The target grind size of the circuits varies between the 90% and 95% passing 500 mesh (32 μm) depending on the feed ore characteristics and operating conditionsIn this scenario, the world pelletizing capacity grew from 350 Mt/year in 2000 to more than 600 Mt/year in 2020. ron ore products and the corresponding use in iron making. (4) Typical(PDF) EVOLUTION AND GROWTH OF IRON ORE
احصل على السعر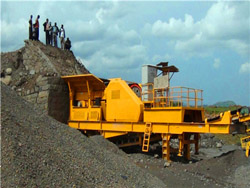
KOBELCO Pelletizing Process
include iron scrap, reduced iron pellets and reduced iron briquettes. Sintered ore is made by partially melting and sintering coarse iron ore 1 to 3mm in size into products having a size of 15 to 30mm. The sintering process uses the combustion heat of coke breeze (fuel). Pellets are made from iron ore that is finerAs part of efforts to reduce anthropogenic CO<sub>2</sub> emissions by the steelmaking industry, this study investigated the direct reduction of industrially produced hematite pellets with H<sub>2</sub> using the Doehlert experimental design to evaluate the effect of pellet diameter (10.5–16.5 mm), porosity (0.36–0.44), and temperature Hydrogen-based direct reduction of industrial iron ore pellets
احصل على السعر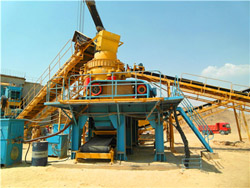
(PDF) Iron ore pelletization ResearchGate
Arrium Australia 0.810 0.810 0.440. 440 Iron Ore. The pelletizing process involves the preparation of ra w materials; the proportioning. and mixing of raw materials; the formation, preheating, anda Flowchart of pellet preparation and analysis of pellets, b green pellets, c Indurated pellets, d X-ray curve of Barsua slime Concentrate showing the various phase (H—Iron oxide (Fe 2 O 3), G—Goethite (FeO (O.H.)), and S—Silicon oxide), and Petrology of e Barsua Iron Ore slime concentrate and the three different size fractions of iron ore Effect of Blaine Number on the Physical and Mechanical
احصل على السعر
Iron Ore Pelletizing Process: An Overview ResearchGate
Figure 2 shows a flowchart of a typical pelletizing plant, highlighting the additive preparation, mixing and pelletizing feed preparation, the balling step, in this case using a disc pelletizerThe pelletization process is the primary consumer of binders in the iron ore industry. The selection of an appropriate binder type and dosage is of critical importance in producing good quality pellets at a reasonable price. Binders accomplish two very important functions in iron ore pelletization: .Iron ore pelletization ScienceDirect
احصل على السعر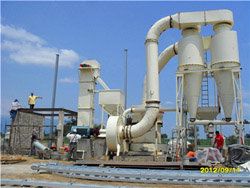
Introduction to Iron ore Pellets and Pelletizing
There are four stages involved in the production of iron ore pellets. These stages consist of (i) raw material preparation, (ii) formation of green balls or pellets, (iii) induration of the pellets, and (iv) cooling, The pelletization process for magnetite ores can be broadly categorized into three sub-processes -raw material preparation, balling and induration, a schematic of process flow is shown in Figure 3Schematic of typical process flow sheet for magnetite
احصل على السعر
A Study on High-Grade Iron ore Beneficiation to Reduce
Iron ore pellets are largely characterized by inherent physical and chemical properties of the ore. Alumina and silica play important roles in determining the productivity of a Blast Furnace. On average, one percent increase in iron content improves productivity by 2% and reduces coke consumption by 1%. Therefore higher iron ore feed content to The iron-making process requires high-quality raw materials, with Fe ≥ 64% and <2% alumina and silica each, to enhance blast furnace productivity at a given energy consumption rate. There is aIron ore beneficiation: an overview ResearchGate
احصل على السعر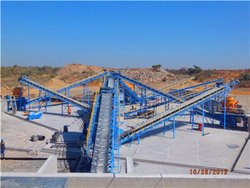
Process flow chart of preparation of pellets ResearchGate
Green pellets of around 18 mm size were made with optimum water content by prolonged hand rolling of moistened iron ore fines of BS -72 mesh size without bentonite as per flow chart (Fig. 1). FIn book: Encyclopedia of Iron, Steel, and Their Alloys (pp.pp 1082-1108) Chapter: i) Direct Reduced Iron: Production; Publisher: CRC Press, Taylor and Francis Group, New York.(PDF) i) Direct Reduced Iron: Production ResearchGate
احصل على السعر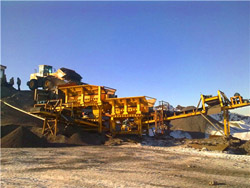
PELLET PLANT environmentclearance.nic.in
The finished product detail of the pellet plant is as below:-Product Capacity Use of finished product Pellets (MT/Annum) 1.2 MTPA Captive use and sale to Market Land Requirement and Land type of project area: The Pellet plant is located adjoining to the Dhedwas Iron ore and associated minerals mine of JSL at village Pur, The sinter plant that converts the iron ore fines into a desirable blast furnace feed, offers an avenue for recycling wastes. One of the several wastes that are produced at an iron and steel plant is the undersized pellet fines, which cannot be directly used in iron making. The present study evaluated the influence of these pellet fines on Utilization of Pellet Fines in the Iron Ore Sintering Process
احصل على السعر- موردي الكرة مقرها وحدة حيدر اباد
- رقم الها تف الشركة بيع كسارة
- السطوح طحن سطح
- industrial laundry washing machine south africa
- تطبيق جديد في القمائن الدوارة، سابقة التجهيز
- ما هي آلة طاحونة
- traditional grinding streaming
- الأبحاث المتعلقة ب ملموسة سحق آلة التعدين
- محطة معالجة خام الحديد
- مطحنة مطحنة الأسطوانة الصحافة كشب في
- Iron Mills Garage En Rockville Md
- معدات سحق الحجارة المستخدمة أراد
- مطحنة تعدين الحجر للبيع جنوب أفريقيا
- كسارة خام الذهب المتنقلة للتأجير
- air operated positive displacement pump manufacturers