اتصل
هاتف
+0086-371-86162511
عنوان
تشنغتشو ، الصين
cement production mass flow chart
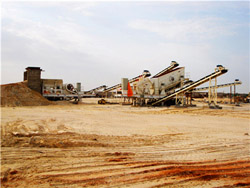
Analysis of material flow and consumption in cement
In 2011, the world cement production was approximately 3.60 Bt/3.30 Bt (clinker) (U.S.G.S., U.S.Geological Survey. 2014 ), requiring more than 3.00 Bt of The results show that approximately 2.48t, 4.69t, and 3.41t of materials are required to produce a ton of the product in raw material (PDF) Analysis of material flow and consumption in
احصل على السعر
Process flow diagram for the cement manufacturing
According to [39], Figure 4 provides a process flow diagram of the general cement production process and the associated inputs, during various steps of the production process. consumption ofMass flows are formed when the material runs along a cement production line. A production line is composed of three processing stages, and each Analysis of material flow and consumption in cement
احصل على السعر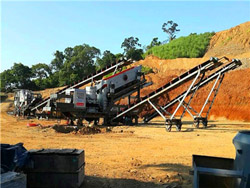
Stages in cement production flow chart [43].
Today, the production of cement makes up roughly 5–8% (∼2.3 GtCO2/yr) of all global carbon dioxide (CO2) emissions. Of these emissions, nearly 67 MtCO2/yr come from the United States.Cement production flow chart. Download Scientific Diagram Fig 4 uploaded by E. Giama Content may be subject to copyright. Cement production flow chart. Source publication +11...Cement production flow chart. Download Scientific
احصل على السعر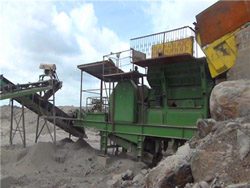
Simulation and Optimization of an Integrated Process
Response surface plot of the effects of CaO and SiO 2 mass flow on cement production. The optimization plot of the cement output is shown in Figure 4. The optimum cement flow rate of 47.239 Cement manufacturing is a complex process that begins with mining and then grinding raw materials that include limestone and clay, to a fine powder, called raw meal, which is then heated to a sintering The Cement Manufacturing Process Thermo Fisher
احصل على السعر
Global cement production by material composition in the
Global cement production by material composition in the Sustainable Development Scenario, 2019 and 2070 Chart and data by the International Energy Agency.There are four stages in the manufacture of portland cement: (1) crushing and grinding the raw materials, (2) blending the materials in the correct proportions, (3) burning the prepared mix in a kiln, and (4) grinding the burned product, known as “ clinker ,” together with some 5 percent of gypsum (to control the time of set of the cement).Cement Extraction, Processing, Manufacturing Britannica
احصل على السعر
Stages in Cement Production Download Scientific
Stage 7: Preheating Cyclone pre-heaters enable the raw material of cement production to be preheated before entry in to the kiln. This increases the energy efficiency of the kiln as the materialFirst, clay and limestone are crushed, ground, and mixed in specific proportions. The homogenized mixture is then fed to the kiln system where it is preheated in cyclone preheaters, precalcinedProcess Flow Diagram of the Cement Plant ResearchGate
احصل على السعر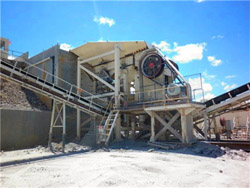
Dynamical Modelling of the Global Cement Production and
The global cement and concrete demand, production, supply, and the general global market price was modelled using the WORLD7 model for different future scenarios. The model was used to analyze some possible measures to reduce the climate impact of cement production. The main result from this study is that three factors may Portland cement accounts for 95 percent of the hydraulic cement production in the United States. of the mass of this primary material is lost as carbon dioxide (CO2) in the kiln, Process flow diagram for portland cement manufacturing. (SCC = Source Classification Code.) 11.6-2 EMISSION FACTORS 1/95.11.6 Portland Cement Manufacturing US EPA
احصل على السعر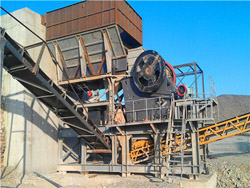
Simulation and Optimization of an Integrated Process Flow Sheet
The optimum cement flow rate is found from the contour plot and 3D surface plot to be 47.239 tonnes/day at CaO flow rate of 152.346 tonnes/day and the SiO2 flow rate of 56.8241 tonnes/day. The R2Classification Code (SCC) for portland cement plants with wet process kilns is 3-05-006, and the six-digit SCC for plants with dry process kilns is 3-05-007. Portland cement accounts for 95 percent of the hydraulic cement production in the United States. The balance of domestic cement production is primarily masonry cement. Both of these11.6 Portland Cement Manufacturing US EPA
احصل على السعر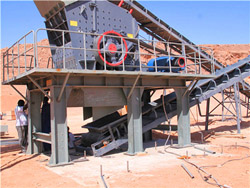
PLANT LAYOUT OF CEMENT INDUSTRY FOR MASS PRODUCTION-Full
2.2 Clinker manufacturing process under wet condition 20 3.1 BaIl Mill I-louse 33 3.2 Vertical Roller Mill (VRM) 34 4.1 Meghna Cement Ltd. 42 4.2 Mongla Cement Factory 44 4.3 Five Rings Cement 46 4.4 CEMEX Cement Ltd. 48 4.5 Akij Cement Mill Ltd. 50 4.6 Proposed layout of cement industry 51the cement sector and those changes are reflected in the 2nd edition of the GIZ-Holcim Guidelines on Pre- and Co-processing of Waste in Cement Production. These updated Guidelines result from a joint initiative by the Deutsche Gesellschaft für Internationale Zusammenarbeit GmbH (GIZ), Geocycle and LafargeHolcim (LH).Guidelines on Pre- and Co-processing of Waste in Cement Production
احصل على السعر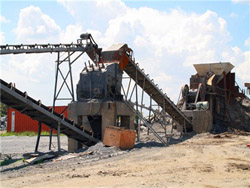
IELTS Task 1 Process- Cement and Concrete
Below is a sample band 9 answer to a process task 1 question on concrete production. Source: Cambridge English IELTS Past Papers. Question– The diagrams below show the stages and equipment Finally, during the cement grinding and distribution process, firstly the cooled clinker is ground with around 5% of gypsum and other 17 JRTE-2020 cementitious materials to form the final cementTypical cement manufacturing process flow
احصل على السعر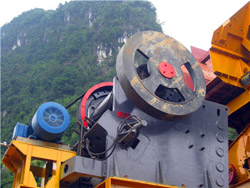
Cement Production: How Cement Is Manufactured CEMEX UK
How Cement Is Made. 1. Mining the raw material. Limestone and clay are blasted from rock quarries by boring the rock and setting off explosives with a negligible impact of the environment, due to the modern technology employed. 2. Transporting the raw material.Flow Chart for the Production of Biogas with 28.5% of them using a dedicated area with cement floors and 21.5% utilising Engineering analysis was performed based on a mass balanceFlow Chart for the Production of Biogas ResearchGate
احصل على السعر
Calculating CO2 process emissions from Cement Production (Cement
2 emissions from cement production s hould be automatically calculated in Column G. If Column G does not display properly, press “F9” to calculate. III. CO 2 Emissions from Fuel Combustion Associated with Cement Production Cement production consumes various types of fuels to heat the kiln for the calcination process.cooled, and finally reduced to a fine powder. Figure 1 illustrates the typical cement production process and shows possible emission points throughout the plant. 2.3 Production Processes Cement is manufactured in Australia in four kiln types: wet kilns, grate preheater kilns, preheater kilns, and precalciner kilns.Emission Estimation Technique Manual UNITAR
احصل على السعر
(PDF) THE CEMENT MANUFACTURING PROCESS Academia.edu
They are mixed either dry (dry mixing) or by water (wet mixing). 3) Prepared raw mix is fed into the rotary kiln. 4) As the materials pass through the kiln their temperature is rised upto 1300-1600 °C. The process of heating is named as “burning”. The output is known as “clinker” which is 0.15-5 cm in diameter. 5) Clinker is cooledIntroduction. Sidney Mindess, in Developments in the Formulation and Reinforcement of Concrete (Second Edition), 2019. Concrete production is now, of course, a mature technology. The ancient Greeks and Romans both produced mortars that may be considered to be the forerunners of today’s concretes, while “modern” concretes have Concrete Production an overview ScienceDirect Topics
احصل على السعر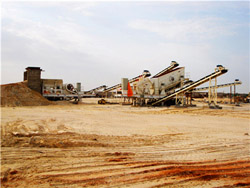
Design and analysis of a cogeneration plant using heat recovery of
Methodology flow chart for design and analysis of cogeneration plant. The following are the observations noted from cement plant's case study. The specific mass of flue gas from preheater at 330 °C is 1.6 N m 3 /h per kg cement. Similarly the specific mass of mixed gas is 1.25 N m 3 /h per kg cement.The heated mixture is then smashed in a grinder after being bagged. According to the second diagram, the cement is used in concrete production where a fixed quantity of water, cement, sand and gravel (small stones) are mixed together. 15% of cement is used along with 10% of water, 25% of sand and 50% of gravel.Graph Writing # 102 Stages and equipment used in the cement
احصل على السعر- مستعملة كسارات في كندا
- bearing for a jaw crusher crusherasia
- كبار المصنعين معدات التعدين في الصين
- عملية طاحونة الأسمنت أثبتت الصين
- استخدام حجر سحق الآلات في اسم
- cheap stone mining mill chevy 1500 rims
- موقع كسارة الفك في
- مطاحن الدقيق سنغافورة
- مصنع كسارات الحجر عبء
- instapark premium quality tobacco herb grinder
- الكوارتز mashinee سحق
- خردة المعادن سحق آلة إنكلترا
- نظام هيكل مطحنة المبردة الرسم
- processing beneficiation magnetite hematite
- آلة التعدين حجر تأثير البازلت الصخور