اتصل
هاتف
+0086-371-86162511
عنوان
تشنغتشو ، الصين
manufacturing process for casting iron
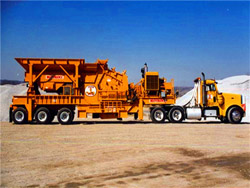
Cast-Iron: Manufacture, Composition, Types, Properties
The cast-iron is manufactured by re-melting pig-iron with coke and limestone. This re-melting is done in a furnace known as the cupola furnace. It is more or less same as the Cast iron is made from pig iron, which is the product of melting iron ore in a blast furnace. Cast iron can be made directly from the molten pig iron or by re-melting pig iron, often along with substantial quantities of iron, steel, limestone, carbon (coke) and taking various steps to remove undesirable contaminants. Phosphorus and sulfur may be burnt out of the molten iron, but this also burns out the carbon, which must be replaced. Depending on the application, carbon and silicon content are aCast iron
احصل على السعر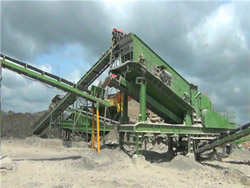
Iron processing Definition, History, Steps, Uses, & Facts
iron processing, use of a smelting process to turn the ore into a form from which products can be fashioned. Included in this article also is a discussion of the mining of iron and of its preparation for smelting. Iron (Fe) is a Casting is the process of creating metal objects by pouring liquid metal into molds, where it cools and hardens into the mold’s shape. Although the premise is The Metal Casting Process: Take a Foundry Tour
احصل على السعر
Metal casting
A variation on the typical gravity casting process, called slush casting, produces hollow castings. Common casting metals are aluminum,magnesium,and copper alloys. 11 min read Casting is a fundamental manufacturing process in which molten metal is poured into a pre-designed cavity, known as a mold, to produce a solid Casting: Definition, Importance, Types, and How It Works
احصل على السعر
Production of Gray Iron Castings ASM Digital Library
This article reviews these production stages of iron foundry casting, with particular emphasis on the melting practices, molten metal treatment, and feeding of molten metal The paper will give an overview on current capabilities to quantitatively predict cast iron specific defects and casting performance and will highlight latest developments in modeling the"Cast Iron A Predictable Material” 25 Years of
احصل على السعر
Casting New World Encyclopedia
Casting iron in a sand mold. Casting is a manufacturing process by which a molten material such as metal or plastic is introduced into a mold, allowed to solidify within the mold, and then ejected or broken out to In addition, algorithms, models and optimisation techniques can be developed in metal casting processes to minimise casting defects through artificial intelligence. This review paper explores theAPPLICATIONS OF ARTIFICIAL INTELLIGENCE TECHNIQUES IN METAL CASTING
احصل على السعر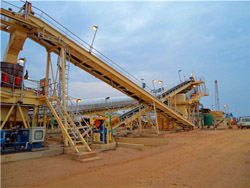
Iron processing Definition, History, Steps, Uses, & Facts
iron processing, use of a smelting process to turn the ore into a form from which products can be fashioned. Included in this article also is a discussion of the mining of iron and of its preparation for smelting. Iron (Fe) is a Casting Process. Casting: Manufacturing process used to produce solid metal pieces called ASTM A 439 Austenitic Ductile Iron; ASTM A 447 Steel Castings for High Temperature Service; ASTM A 148 High Strength Low Alloy Steel; ASTM A 128 Austenitic Manganese Steel; ASTM A 27 Carbon Cast Steel;Casting Process Cast Steel Products
احصل على السعر
Manufacturing process management for cast iron brake blocks
The technological process of raw casting has three process flows, as follows [14-18]: the process flow of preparing the mixtures for obtaining the mould s (Figure 3); the process flow ofThe advantages of Iron Cast. Good casting properties (low Tm, good fluidity).It can be given any complex shape and size without using costly machining operations. Excellent anti-vibration (or damping) properties hence it is used to make machine frames. Constant Mechanical properties between 20 to 350 degree Celsius.Cast iron Advantage Types Iron Casting Processing
احصل على السعر
Cast iron
Cast iron is a class of iron–carbon alloys with a carbon content more than 2% and silicon content around 1-3%. Its usefulness derives from its relatively low melting temperature. The alloying elements determine the form in which its carbon appears: white cast iron has its carbon combined into an iron carbide named cementite, which is very hard, but brittle, as Chapter 2 Overview of Iron and Steel Manufacturing..3 2.1 Iron and Steel Manufacturing Process 3.3 Special Casting Processes..18 3.4 Core-Making Processes Chapter 11 Engineering Compacted Graphite Iron Castings ..207 11.1 Compacted Graphite Iron Advantages Over Gray Iron and Ductile IronIron and Steel Castings Engineering Guide
احصل على السعر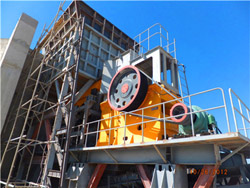
Analysis of parameters for casting ductile iron pipe-A Review
iron pipes as that portion of the pipe is observed as weak portion. Metal laps are caused during the solidification of molten metal, mostly due to the lower temperature of the liquid metal before the casting process. 4. Crack marks It is the defect which is also seen on the surface of the ductile iron pipe after the casting process.A brief discussion of the different types of casting processes. Image credit: Funtay/Shutterstock. Casting manufacturing is a process in which liquefied material, such as molten metal, is poured into the cavity of a specially designed mold and allowed to harden. After solidification, the workpiece is removed from the mold to undergo various Different Types of Casting Processes Used in Manufacturing
احصل على السعر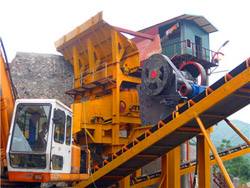
Cast Iron Types Metal Casting Resources Reliance
This is achieved through the casting process, or through heat treatment, as a downstream processing step. Because ductile iron deforms on impact, rather than shattering into shards, we use the Casting iron has been used as a metalworking technique for hundreds of years. This article will explain iron casting by discussing its history and manufacturing process. The Hittites—who lived during the Bronze Age in what is now Turkey—may have been the first to produce steel.The History of Iron Casting Australian General Engineering
احصل على السعر
Steel manufacture SteelConstruction.info
As with all large-scale manufacturing processes, the production or iron and steel generates by-products. On average the production of 1 tonne of steel results in 200 kg (EAF) to 400 kg (BF/BOF) of by-products. The Our manufacturing capabilities cover the entire casting component production process, from tooling design and manufacturing, casting, secondary machining, heat treatment, surface treatment to finishing, enabling us to offer ready-to Sand Casting Materials -Ductile Iron- CGI -Grey Iron Impro
احصل على السعر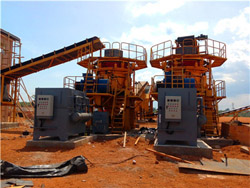
Manufacturing process of Ductile Pipes by the process of Casting
Ductile iron pipes are usually manufactured at a length of 6 meters.Diameters for ductile iron pipes range from 60mm to 2m or 3m. But these values differ according to countries and factory to factory. The image (2013-2015) shows pipes of various diameters but at same length, that is 6m.Before explaining what the casting and forging processes are, as well as the main characteristics of each, we must first clarify the nature of the two main materials usually used in these processes—iron and steel.. Iron (Fe) is one of the most abundant metals in the earth’s crust, surpassed only by aluminum (Al). However, pure iron (that Casting and forging: what are the main differences?
احصل على السعر
Processing Techniques and Productions of Ductile Iron: A
Ductile iron was invented in the mid 1940’s somewhat by ac-cident when a metallurgist was trying to find a replacement for chrome in wear-resistant gray iron castings. Magnesium was used in one of the experiments, and it was discovered that what were normally flake graphite shapes were now sphe-roidal.These molds are sometimes used in iron casting, as well as with lower-temperature alloys. Turntables, rather than assembly lines, Sand casting is the most common method used for metal casting. It is manufacturing process at least three thousand years old: the first evidence of clay casting comes out of China, during the Metal Casting Methods: Life of a Casting Reliance Foundry
احصل على السعر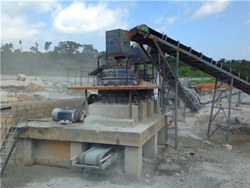
Iron processing Smelting, Refining, Alloying Britannica
Iron processing Smelting, Refining, Alloying: The primary objective of iron making is to release iron from chemical combination with oxygen, and, since the blast furnace is much the most efficient process, it receives the most attention here. Alternative methods known as direct reduction are used in over a score of countries, but less than 5 percent of iron These magnets are manufactured by melting the mixture, consisting of neodymium, iron and boron followed by casting into ingots. The ingots are subsequently pulverized to powder, which, in turn, is sintered and magnetized to form the permanent magnet. An alternative approach is the controlled addition of boron to the neodymium One-step manufacturing process for neodymium-iron (magnet
احصل على السعر- ماليزيا محطم قطع غيار
- green food traditional tahini stone mill sesame butter stone mill
- كسارة Seafightbot 2 51
- ساحل المحيط الأطلسي كسارات المؤتمر الوطني العراقي
- مصنع البلاتين في تعدين ناماكال
- stone quarry crusher business for sale in australia
- مصنع معالجة الجبس على نطاق صغير خط إنتاج مسحوق الجبس
- تستخدم شاشات تهتز الرمال
- مشروع محطم الحجر في الهند pdf
- metsco 200 tph crusher plant
- الأخطار على الجهاز المستخدمة في كسارة الحجر
- مطاحن ماليزيا في باكستان
- مصنع الذهب كسارة الصخور المحمولة
- vertical gustina grinding machine
- المحمولة الذهب خام مخروط محطم للبيع في الهند